The Artec “AS” Series parallel shaft gearbox is engineered for high-speed performance and reliability. Each unit is designed and manufactured to meet the latest AGMA and API standards (or to custom requirements upon request). Artec delivers efficient and robust parallel shaft gearboxes for demanding industrial applications.
Get a Rapid Same Day Quote!*
Applications
- Oil and Gas
- Power Generation
- Petrochemical Industry
- Energy Recovery Systems
- Testbeds and Research Facilities
Freestanding Gearbox Design Features
- Rigid steel casing construction for maximum durability
- Inspection covers for easy maintenance and service
- Available gear ratios: Single-stage 1 < 10
- Single or double helical gears engineered to API and AGMA standards
- Hydrodynamic or tilting pad bearings for optimal load support
Top View
Bottom View
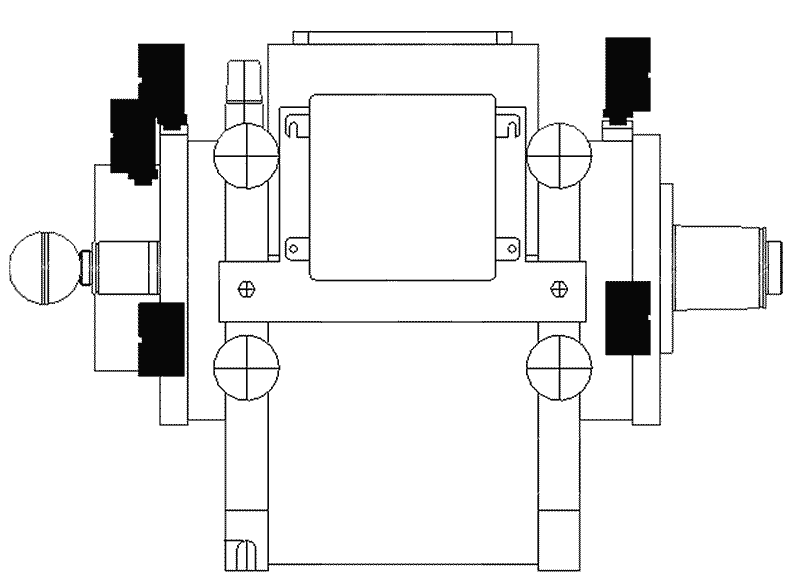
AS-Series Parallel Shaft Gearbox Design Details
Optimized Gear Rotor Profiles
Elastic deflection and thermal gradients can distort tooth contact. Artec engineers apply flank grinding modifications to maintain perfect load distribution across all operating conditions, ensuring consistent performance in high-speed environments.
Journal Bearings
We use two-, three-, or four-lobe pressure-lubricated journal bearings, with optional direct-lubricated tilting pad bearings for high-velocity shafts. Each design ensures excellent rotor stability and minimal energy loss.
Thrust Bearings
Standard tapered land thrust bearings are used, with optional tilting pad bearings and direct lubrication if required by load or application.
Instrumentation
Standard Monitoring Options:
- RTDs or thermocouples on each radial bearing
- RTDs or thermocouples on each thrust bearing (loaded/unloaded sides)
- Mounting provisions for dual shaft-vibration probes (per bearing)
- Accelerometer mounting locations on the casing
- Keyphaser option available upon request
- Additional sensors based on project needs
Precision Housing & Tooth Alignment
Our gearboxes feature offset rotor configurations in a two-piece welded steel housing for easy service access. Gears are typically carburized, hardened, and precision-ground with helical profiles. Lead modifications account for torsional and thermal deflection, maintaining optimal gear mesh and minimizing vibration.
Key Features:
- Optimized center distance and tooth width
- Profile modifications for distortion compensation
- Engineered for stable rotor dynamics
- 4-point mounting base for simplified alignment
- Single or double helical gear toothing
Monitoring Systems
Available monitoring systems include RTDs and vibration sensors compliant with API 670. All systems are designed for integration with customer-specified control panels and diagnostics tools.
*Same-day quote available in most cases during business hours and depending on time of request.