As a custom gearbox supplier, ARTEC has developed a twin screw extruder gearbox system engineered for extreme torque and axial load conditions. Designed for synchronous operation, these high-torque gear units incorporate a double power-splitting system and specialized high axial load thrust bearings to meet the demands of complex extrusion processes.
ARTEC’s robust AEX Series twin-screw extruder gearboxes are optimized for super high-density torque applications in food processing and chemical industries. These newly engineered transmission drives deliver maximum reliability for mission-critical continuous duty.
Technical Parameters:
Model / Item |
Main Motor |
Reducer Ratio |
Rated Output Speed |
Torque |
Torque Factor |
Axial Load |
AEX192CR |
373 kW |
105 rpm |
17 rpm |
204 kNm |
28.8 Nm/cm³ |
6000 kNm |
AEX (range 130–200mm) |
As requested* |
--- |
--- |
Up to 220 kNm |
--- |
--- |
*We can provide customer-specific solutions up to 220 kNm.
**Torque factor = torque divided by the cube of the center distance between the screws.
ARTEC’s AEX Counter-Rotating and Co-Rotating Gearboxes:
- Transmit power from the motor to the extruder screws
- Reduce motor speed to target screw RPM
- Maintain accurate angular screw timing
- Absorb high thrust loads from extrusion forces
- Compact, integrated design with high-strength steel
- Ground helical gears and optimized tooth geometry for quiet, smooth operation
- High efficiency with minimal rotating mass
- Built for long-term reliability
The AEX gearbox series supports screw axle base sizes from 130 mm to 200 mm, with torque and output speeds tailored to each application’s requirements.
All gear teeth are case-hardened and precision-ground, designed to accommodate bending and torsional loads. Backed by decades of expertise in high-speed industrial drives, ARTEC ensures each AEX twin screw extruder gearbox meets the most demanding performance standards.
The gearbox system features a reduction input section and a distribution output section:
- The reduction stage uses a conventional helical gearbox, adapted from Bonfiglioli’s standard reducer program, to reduce the motor’s input speed.
- The distribution section takes input from a single shaft and splits it evenly across two parallel output shafts. Torque is split 50% and 25%/25%, then recombined for balanced power distribution.
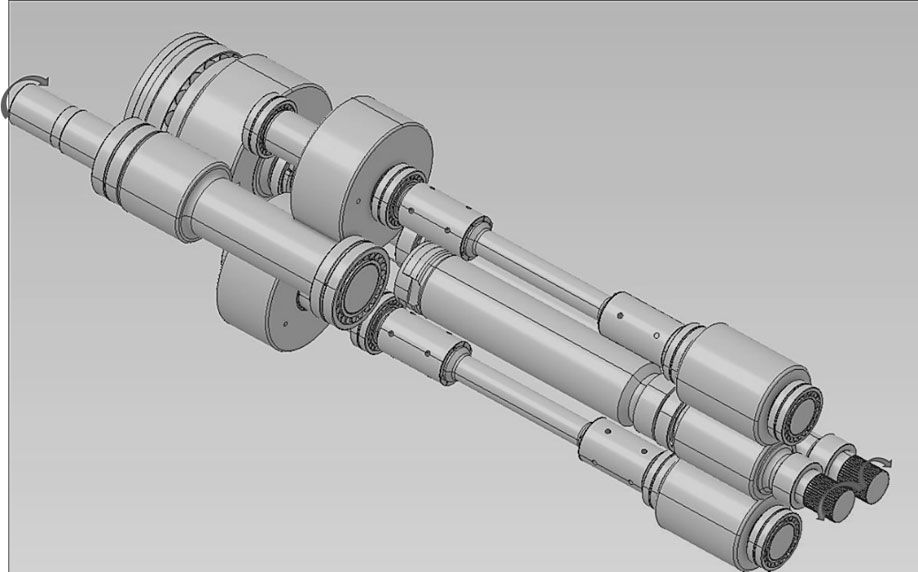
The AEX gear units include high-load axial tandem bearings and self-aligning roller thrust bearings—stacked in layers of up to eight—for managing extreme axial loads from the screws.
The housing is made from thick, rib-reinforced fabricated steel, engineered to contain all internal forces and ensure long-term mechanical integrity.
A top-mounted VSD drive motor is aligned to the gearbox’s reduction section and features an over-torque safety coupling that disengages if limits are exceeded.
A fully integrated splash and pressure lubrication system ensures reliable operation. The gearbox casing doubles as an oil reservoir, and an electric pump circulates oil to all components.
Condition Monitoring Systems
- Built-in torque meter to monitor torsional load and vibration
- Through shaft features a real-time axial load cell
- Tandem output shaft includes an eddy current probe to monitor bearing wear and alignment
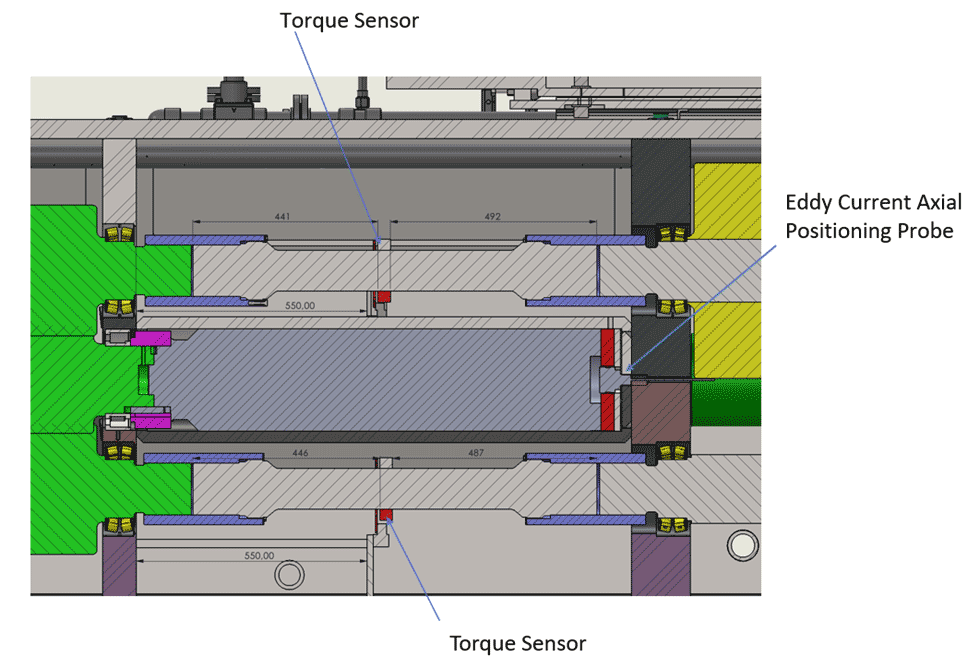
- Two external accelerometers monitor bearing and gear mesh frequency
- Oil system includes a MetalSCAN 3500 debris sensor for predictive maintenance
- Temperature and pressure systems manage oil cooling and flow
- Filter monitoring tracks differential pressure for proactive service intervals

All ARTEC AEX gear units are individually tested and verified to meet continuous performance standards. With this new generation of twin screw extruder gearboxes, ARTEC delivers unmatched power transmission and reliability for next-generation processing systems.